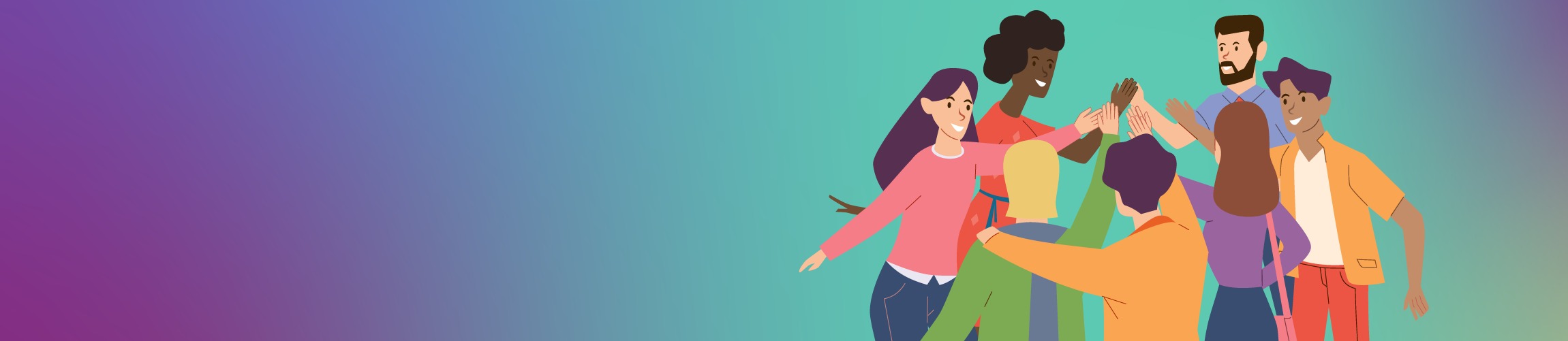
Lean & Six Sigma Simulations:
Where Process Improvement Takes Flight
Lean Six Sigma Simulations and Games are the ultimate training ground for building confidence and mastery. Whether tackling projects, uncovering root causes, or applying DMAIC tools, simulations provide a hands-on way to refine your skills—bridging the gap between theory and real-world application in a risk-free environment.
Why Choose Simulations?
Lean & Six Sigma simulations go beyond teaching tools and methodologies—they solidify comprehension, grow confidence, and build critical thinking skills. By tackling real workplace challenges in a risk-free setting, students learn to choose the right tools with confidence and apply improvements effectively. Plus, when learning feels like a game—engaging, interactive, and hands-on—students stay motivated, grasp concepts faster, and build lasting skills.
Reinforce Learning: Strengthen understanding of tools and methods.
Boost Confidence: Solve problems in a safe environment.
Build Critical Thinking: Learn to choose the right tools intuitively.
Real-World Scenarios: Tackle workplace challenges risk-free.
Sustain Improvements: Drive results long after training.
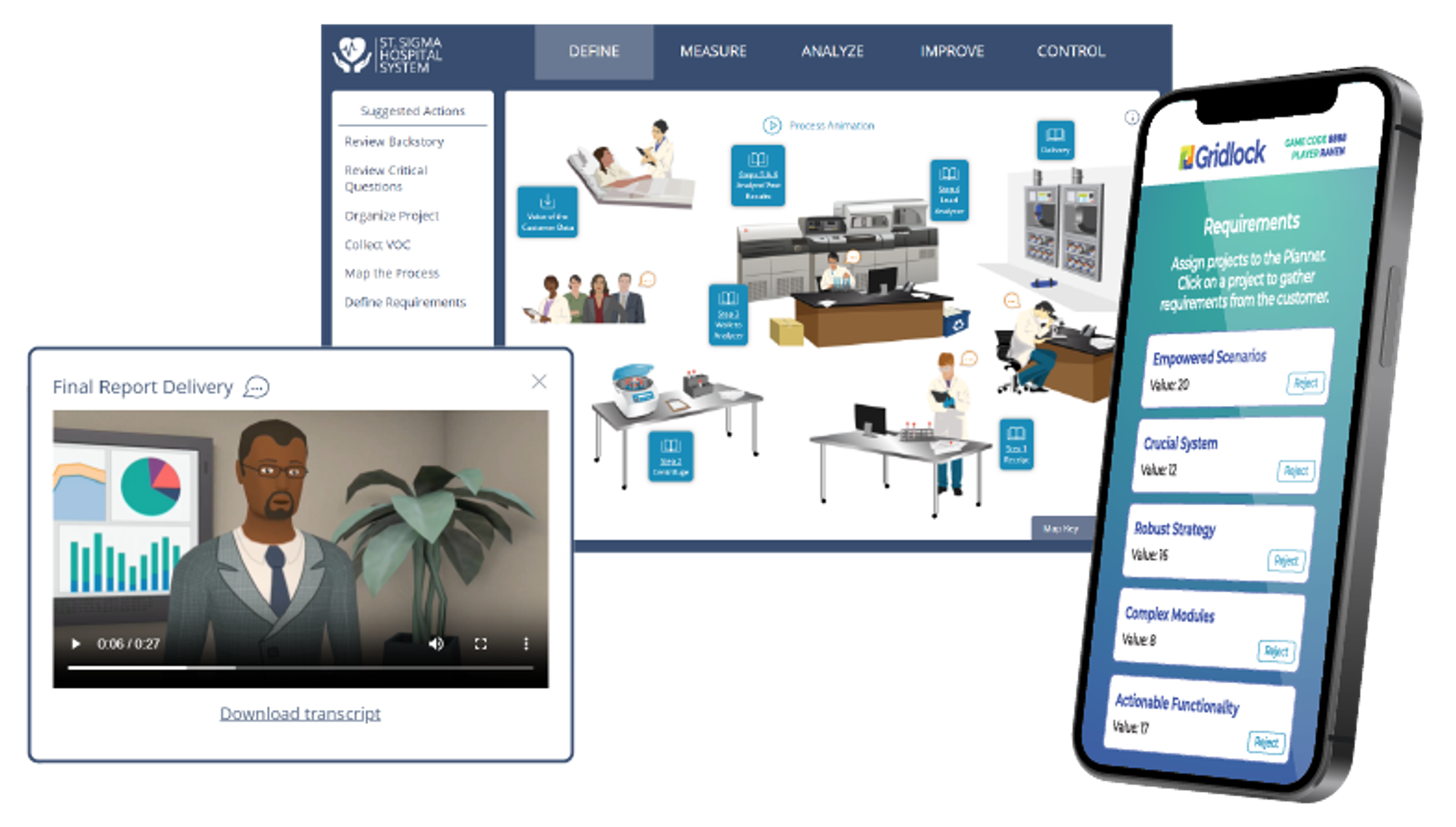
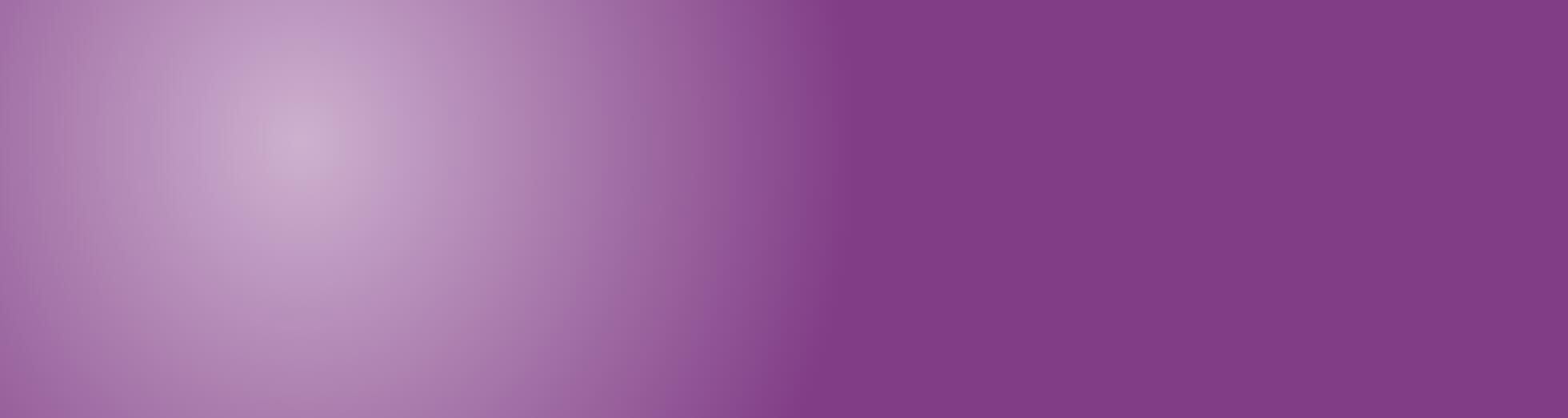
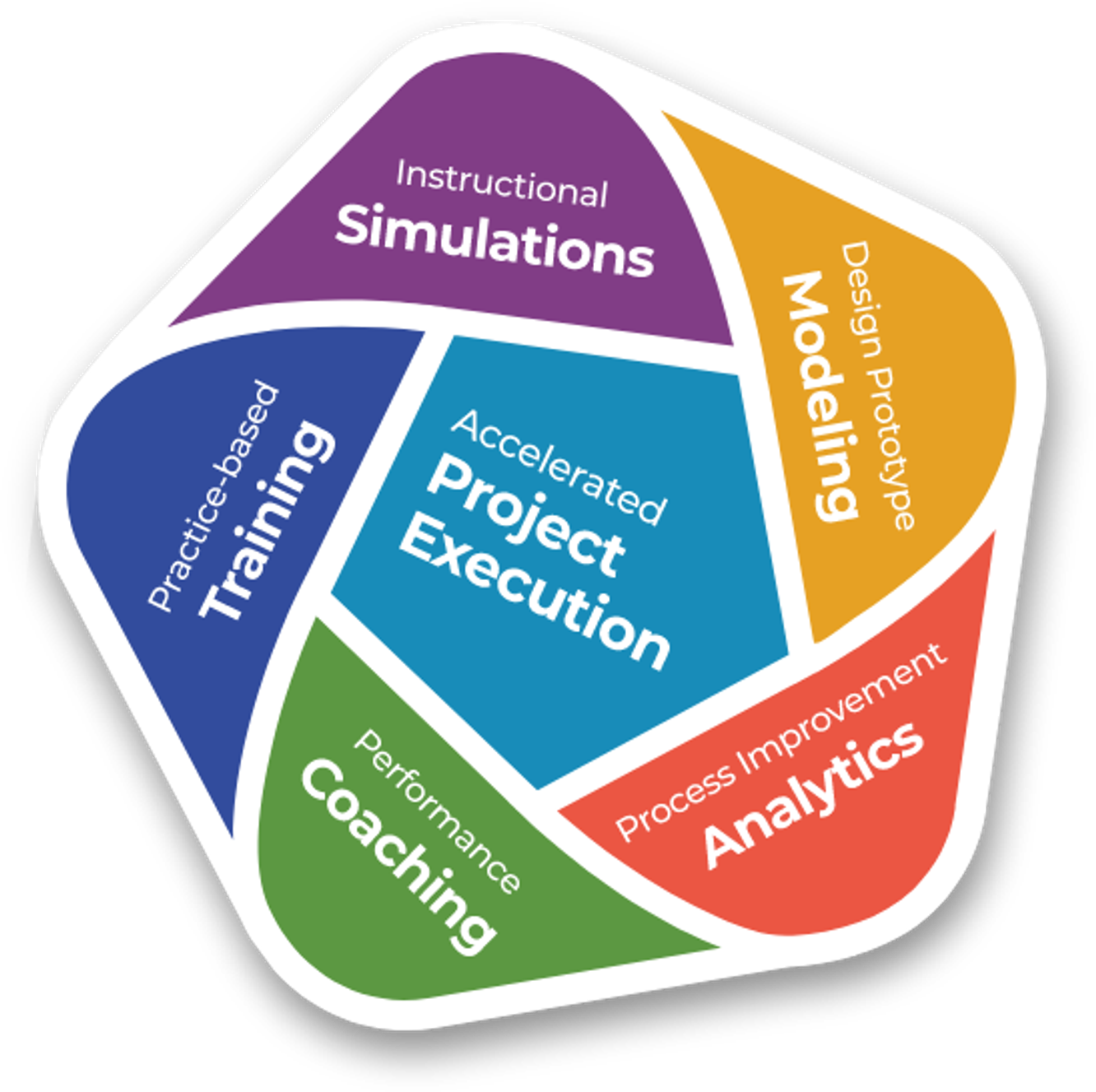
Increase Comprehension and Confidence with Simulations & Games
Lean Six Sigma is more than a set of tools—it's a structured problem-solving methodology that drives real-world improvements. MoreSteam's Enterprise Process Improvement Model helps organizations build a data-driven, problem-solving culture by reinforcing Lean practice and Six Sigma techniques.
A key component of this model is training simulations. These hands-on experiences allow learners to apply DMAIC tools, process design strategies, and problem-solving techniques in a risk-free environment. By completing simulated projects, learners gain the confidence, critical thinking skills, and practical experience needed to excel in real-world process improvement initiatives.
Break Through the Barriers of Continuous Improvement Adoption
Demonstrate the Impact of Lean
From stakeholders to project teams, our suite of Lean Simulations and Games can demonstrate the true impact of Lean improvements.
Showcase the power of Lean to executive teams
Introduce Lean to a wide audience quickly
Help your team gain a deeper understanding of Lean improvements
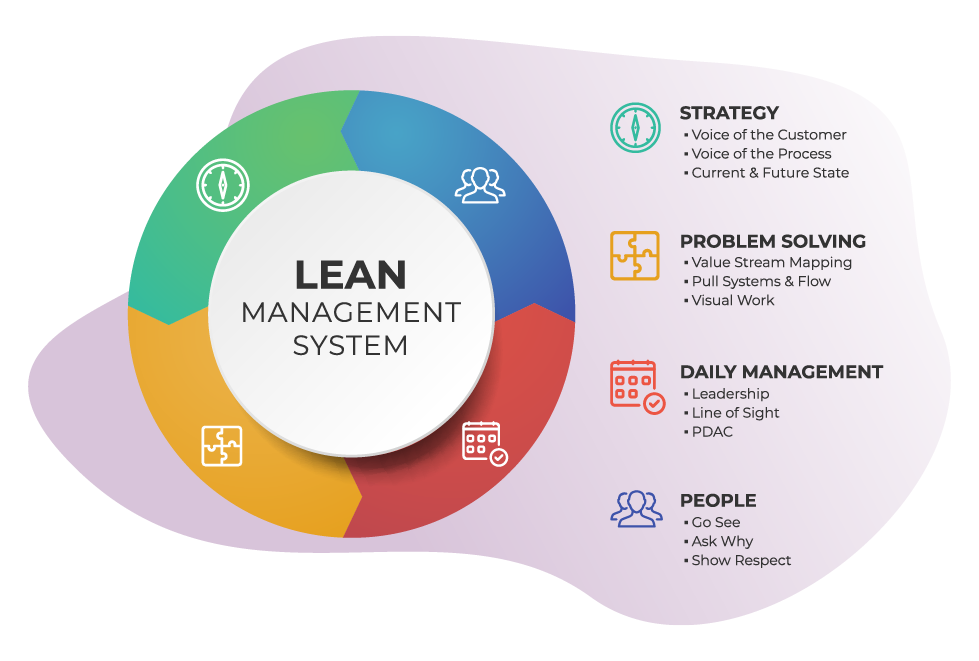
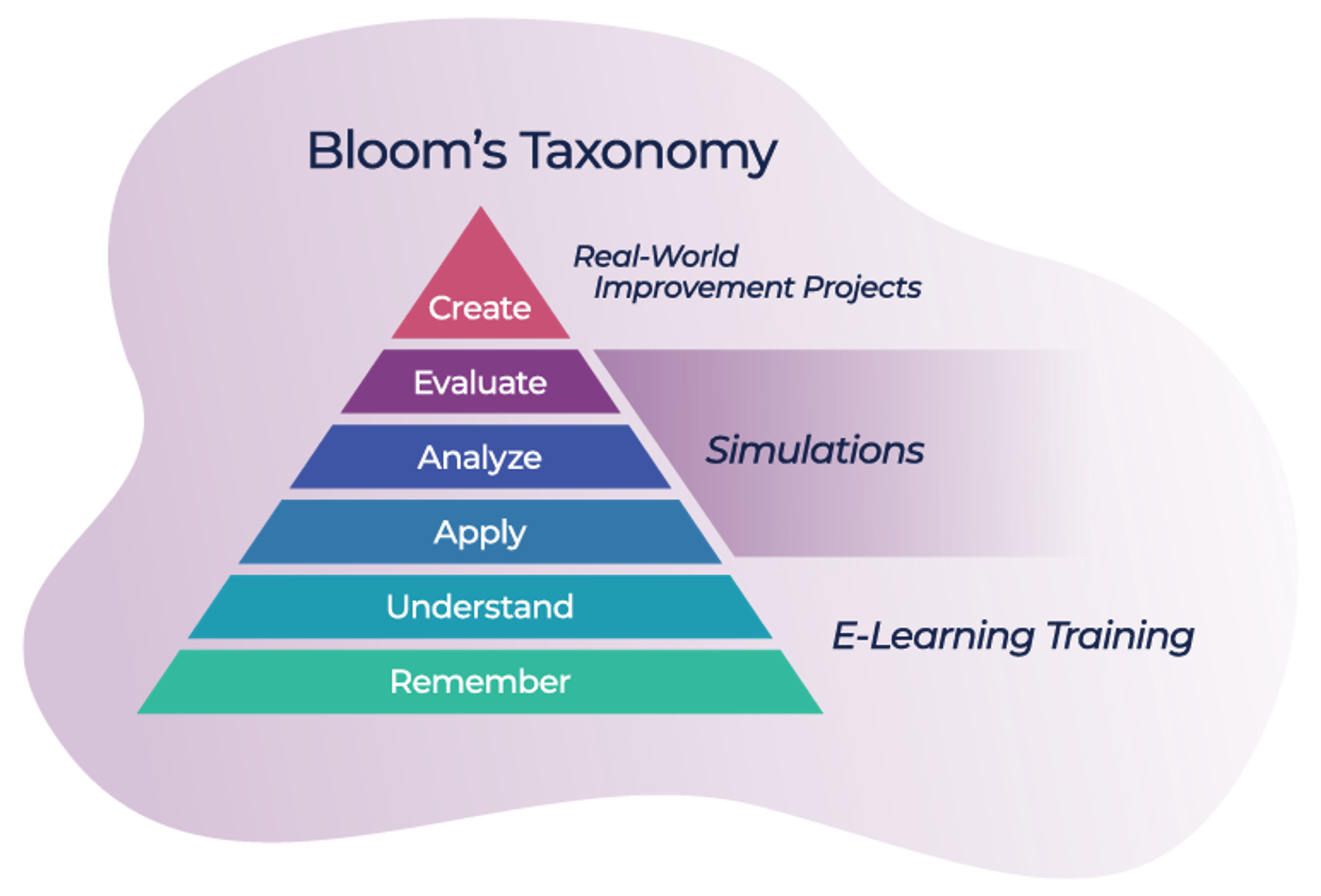
Close the gap between training and project execution
Create a deeper understanding of DMAIC with a step-by-step simulated project integrated with training or as a capstone project.
Enhance comprehension of the DMAIC Process
Increase confidence in problem-solving capabilities
Solidify understanding of when and how to apply each tool
A MANUFACTURING PROJECT SIMULATION focused on applying DMAIC to investigate variation, test solutions, and improve process performance.
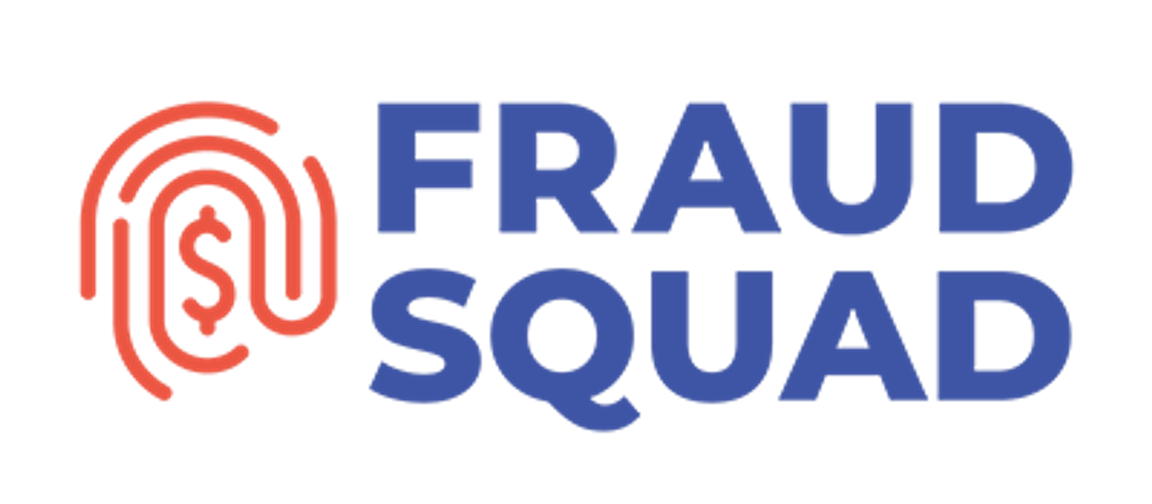
VISIT A VIRTUAL GEMBA in a financial setting to understand the importance of site-inspection and data collection.
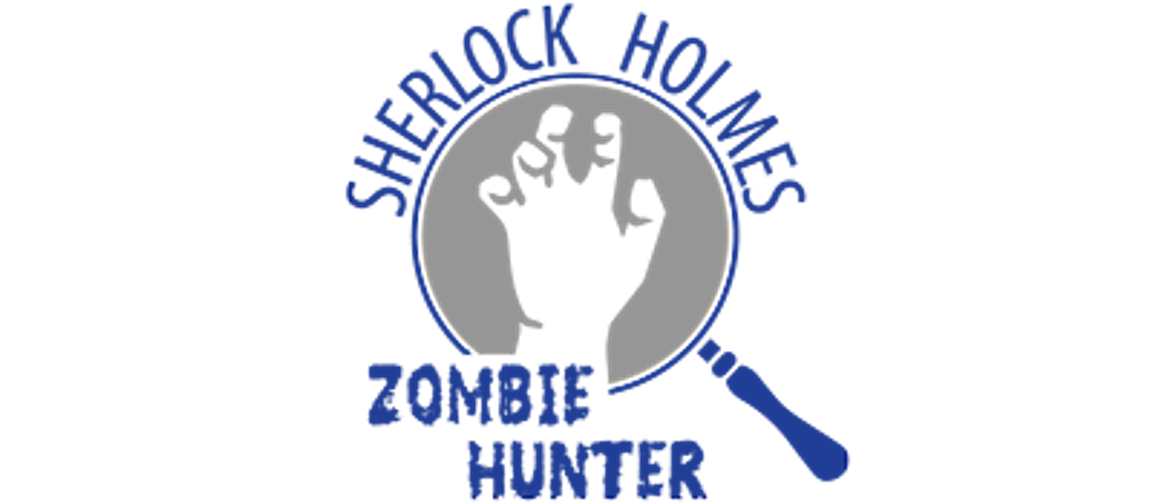
A CAPSTONE PROJECT facilitated over one day and focused on investigative DMAIC problem solving.
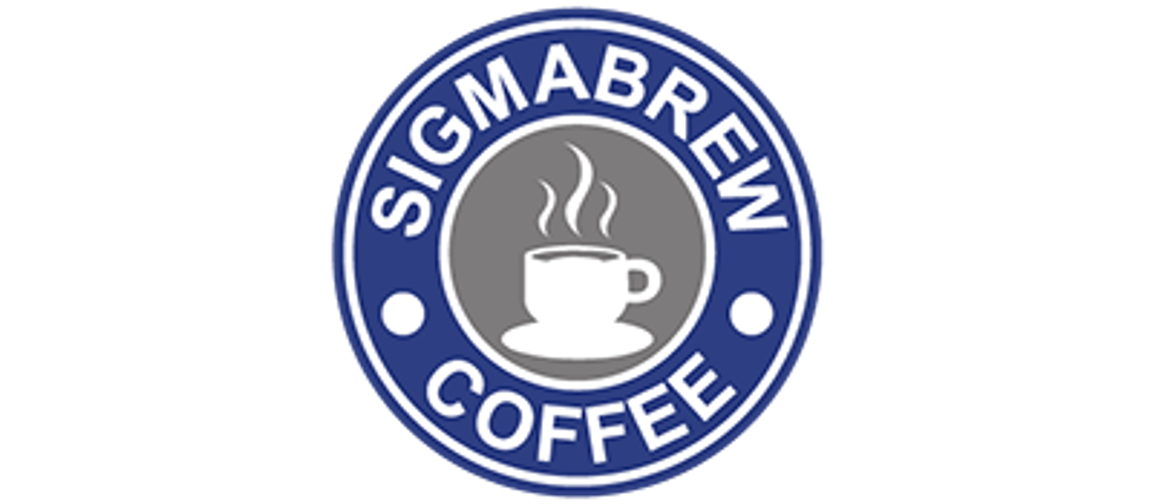
A CAPSTONE PROJECT focused on each aspect of the DMAIC Process facilitated over 2-3 days.
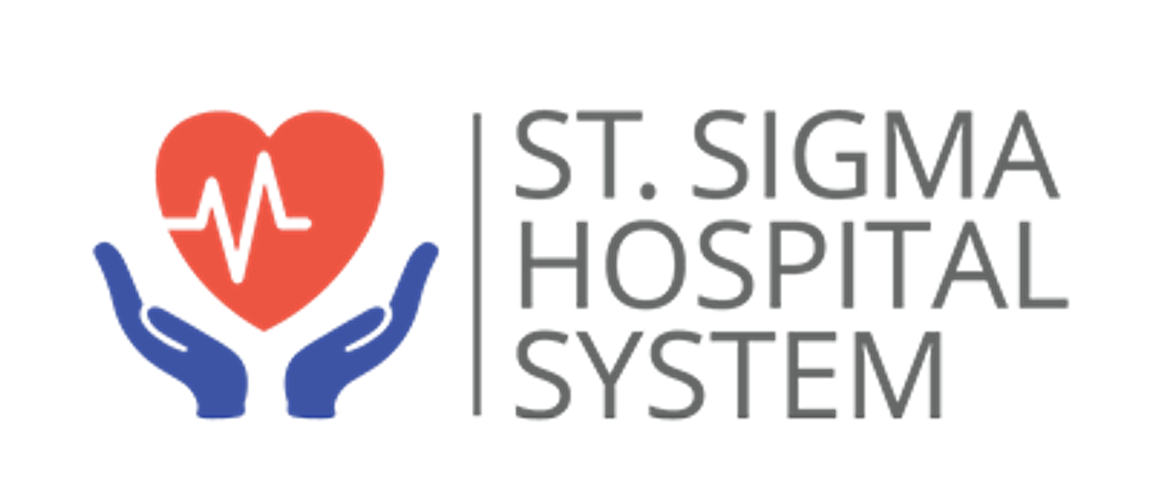
VISIT A VIRTUAL GEMBA to understand the importance of site-inspection and data collection.
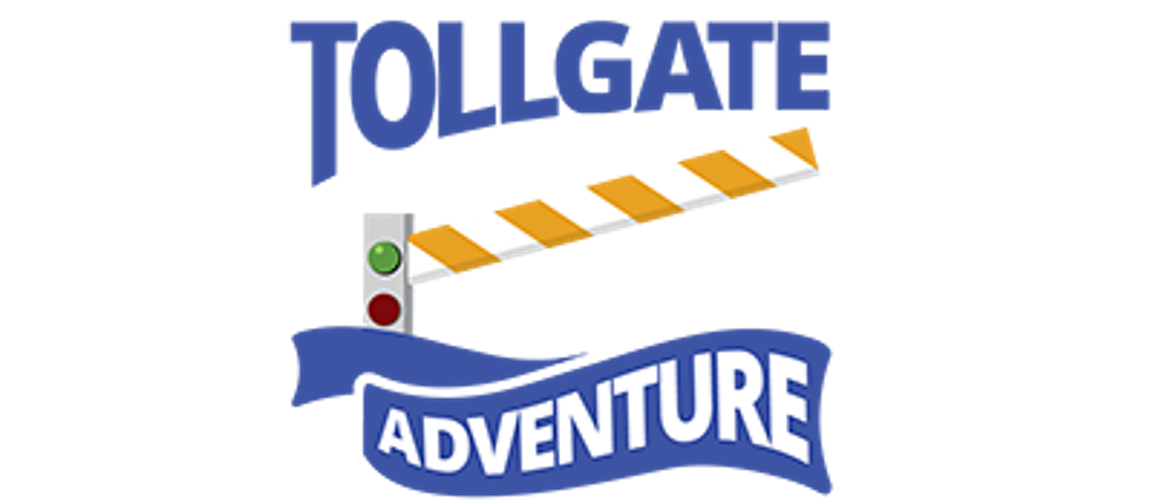
A DMAIC TOLLGATE ROLE-PLAY simulation to lead teams through a series of project tollgate reviews.
Equip your team with critical skills for process innovation
The future of process work demands design thinking and process modeling. Without these skills, teams risk slower progress, higher costs, and missed opportunities to innovate. Simulations provide hands–on experience to teach these critical skills, helping your team adapt, iterate, and deliver impactful improvements quickly.
Speed up problem-solving with focused iteration
Optimize processes without disrupting operations
Reduce costs by identifying improvements upfront
Gain insight and experience with Lean Six Sigma Process Design
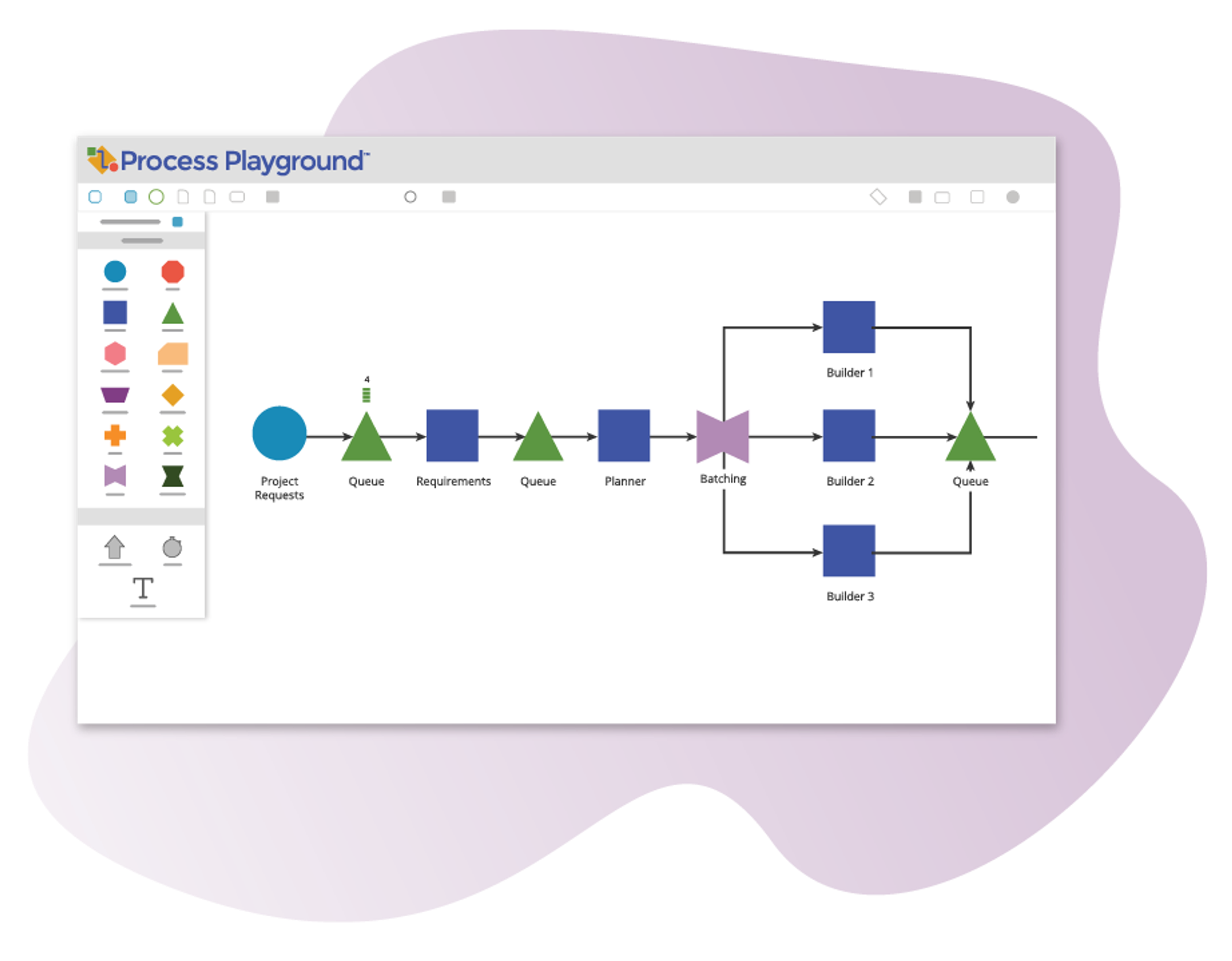
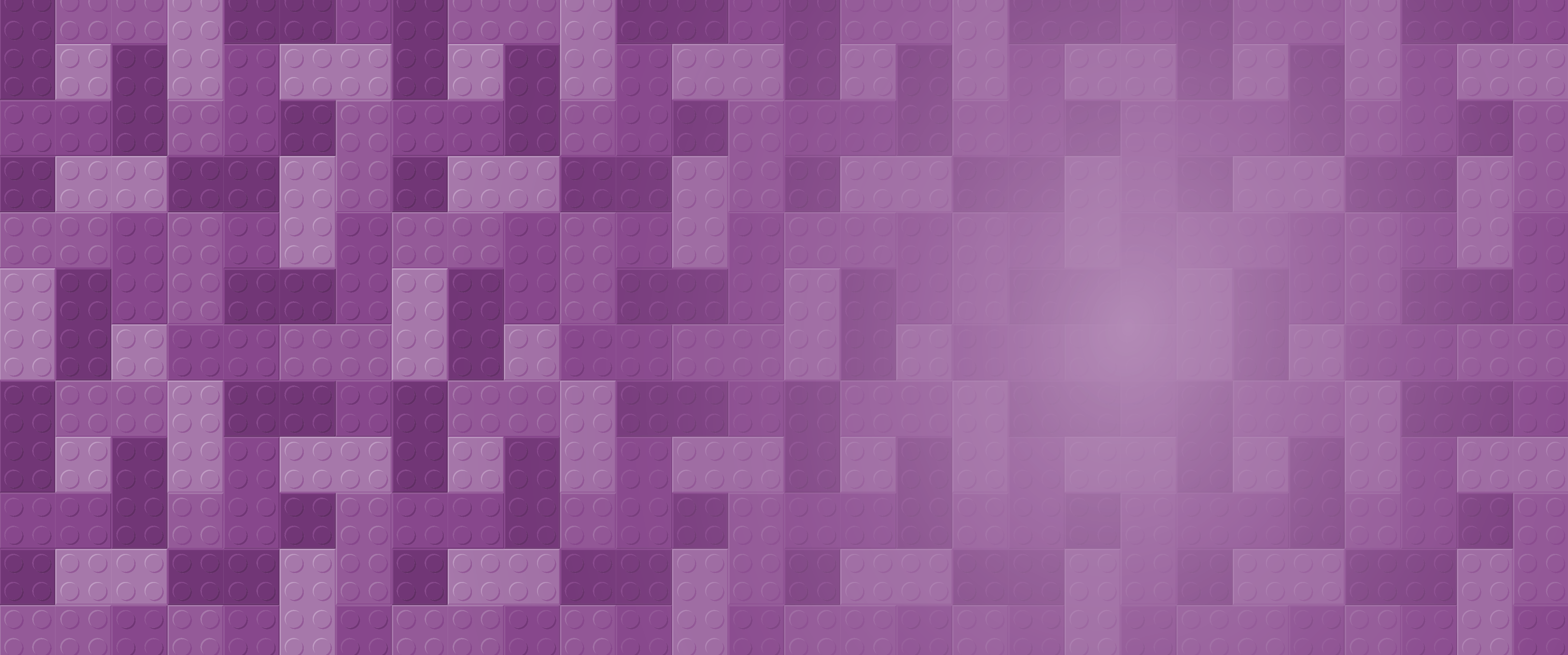
Gridlock vs. LEGO Simulation
Lean Games: A More Flexible Way to Train Lean Teams
Looking for the best way to teach Lean and Six Sigma concepts? While the Lean LEGO simulation has been a go-to for years, MoreSteam's Gridlock Simulation offers a modern, scalable, and engaging alternative for today's teams to teach Lean.
The Lean LEGO simulation relies on physical bricks to teach basic Lean principles. However, it's limited by its setup requirements, in-person format, and the use of abstract scenarios that don't mirror real-world processes.
Gridlock, on the other hand, is a fast-paced Lean simulation that plays like a game—making it both educational and fun. It immerses participants in real-world process challenges, encouraging collaborative problem-solving and Lean thinking in action. Designed for in-person, remote, or hybrid teams, Gridlock provides a flexible, scalable way to teach Lean principles—turning process improvement into a fun and impactful experience for everyone in your organization.
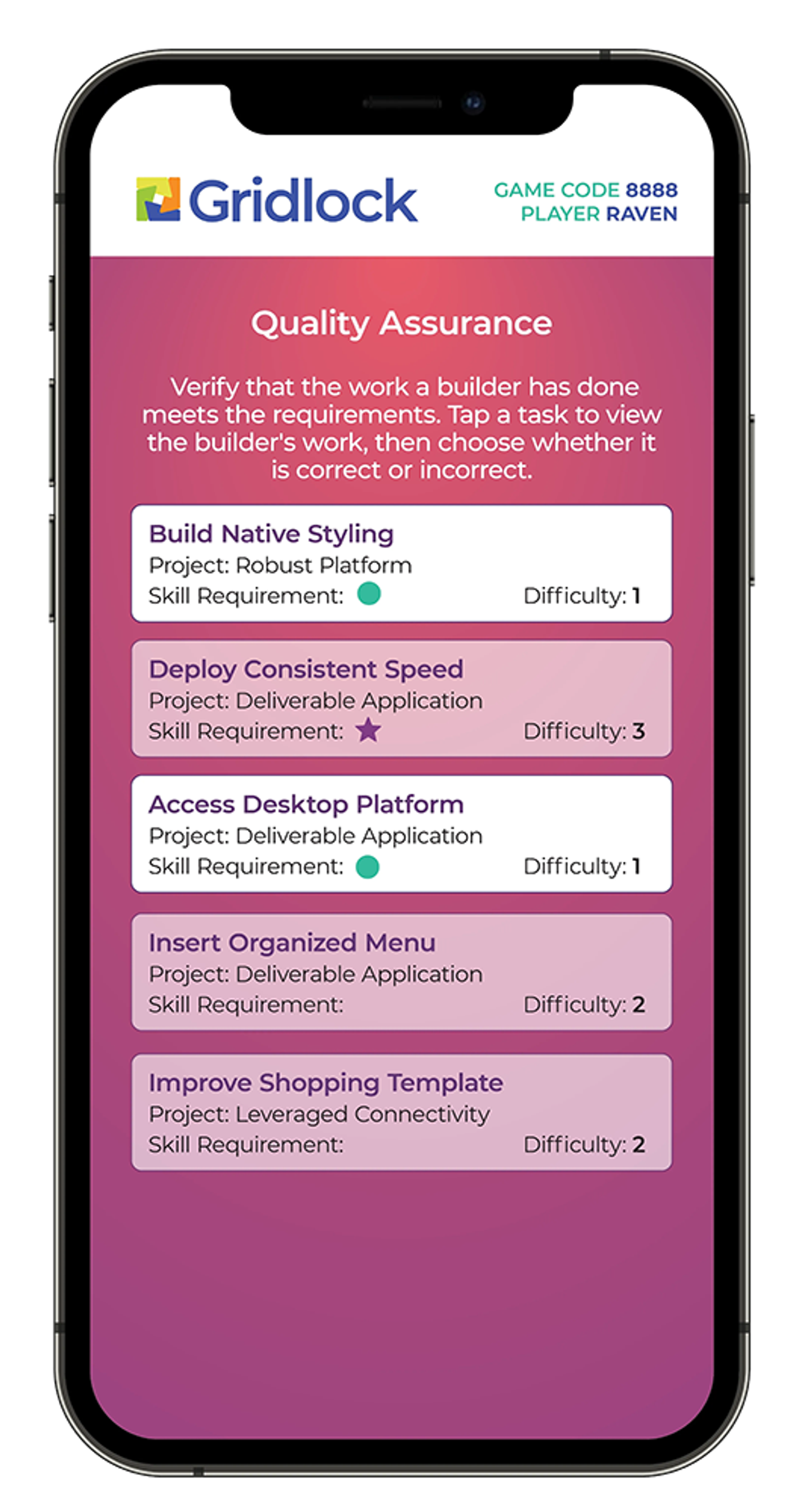
Resources to Support Lean Six Sigma Simulations
MoreSteam provides industry-leading Lean Six Sigma Games and Simulations to help teams practice problem-solving in a risk-free environment. Explore more resources to get the most out of your simulations and enhance your Operational Excellence training.