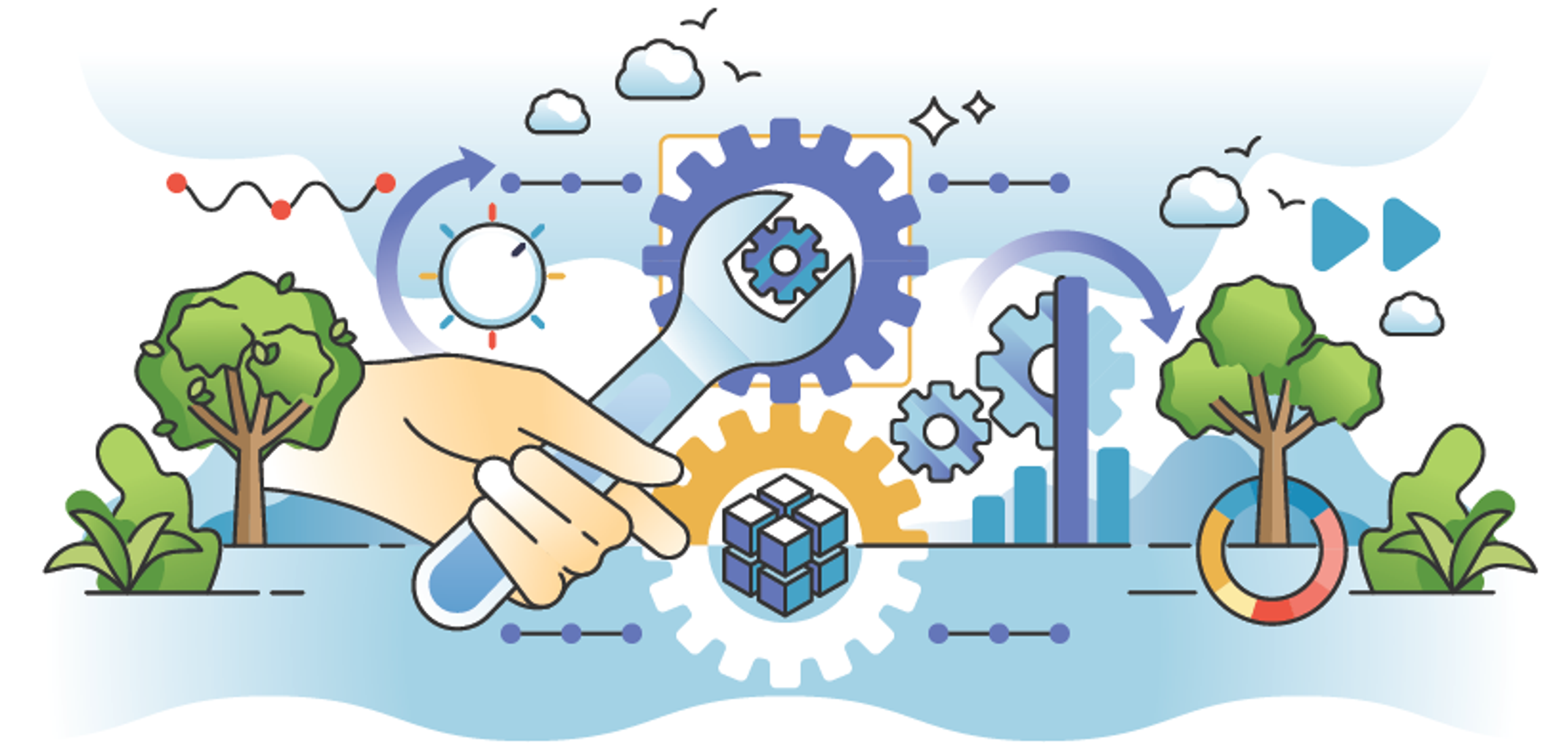
Sustainability: It’s Not a Choice, But a Responsibility
July 8, 2024In today’s business landscape, sustainability isn't just a buzzword – it's a necessity for organizations worldwide. Sustainability seeks to protect our natural resources from depletion, maintain ecological balance, and ensure a better quality of life for future generations. As the global community continues to push for more eco-friendly practices, it is imperative that businesses not only adopt these practices but also find innovative ways to further integrate sustainability into their operations.
When we think of Lean Six Sigma, we often associate it with improving the processes in our business operations. However, what often goes overlooked is that organizations and individuals can use these same LSS methodologies to advance sustainability practices.
- Lean methodology focuses on reducing waste and efficiently utilizing resources to create better process flow and maximize customer value.
- Sustainability aims to protect our natural resources from depletion, maintain ecological balance, and enhance the quality of life for future generations.
- Lean Six Sigma and sustainability go hand-in-hand. The same LSS problem-solving methods that you use in your business operations are instrumental in achieving your sustainability goals.
By blending Lean methodologies with sustainability efforts, businesses can revolutionize their processes and play a pivotal role in conserving resources and safeguarding our environment for years to come.
There’s No DOWNTIME to Waste
At the core of Lean Six Sigma are the eight wastes, or areas that defects are most likely to occur: defects, overproduction, waiting, non-utilized resources, transportation, inventory, motion, and excessive processing (which gives us the acronym DOWNTIME).
- Defects: When a product or service fails to meet customer requirements or expectations, it results in mistakes.
- Overproduction: When production (or service delivery) exceeds customer demand, it can lead to wasteful excess inventory.
- Waiting: This occurs when processes are delayed due to queues between steps.
- Non-Utilized Resources: When employees are underutilized and not engaged in continuous improvement efforts.
- Transportation: Unnecessary movement of products or process-related elements contributes to waste.
- Inventory: Overproduction often results in excess inventory, tying up valuable capital and storage space.
- Motion: Excessive movement, particularly by employees, can be wasteful.
- Excessive Processing: When product or service features exceed what the customer is willing to pay for.
These wastes not only hinder operational performance but also contribute to environmental degradation. For instance, overproduction occurs when products are produced (or services delivered) at a rate that exceeds customer demand.
While “too much” might seem better than “too little,” this can lead to a significant amount of excess waste. Through a sustainability lens, the overproduction of man-made materials, like plastic, for example, can significantly increase the risk of damaged or obsolete inventory ending up in overcrowded landfills. Many of these materials do not biodegrade naturally or quickly, causing severe pollution and environmental damage. The damage caused by this pollution includes ocean contamination, clogged drains, transmitted diseases, increasing respiratory problems from burning, harming animals that consume waste unknowingly, and stunted economic development.
To grasp the significance of this waste issue, consider that global waste production is projected to surge by 70% over the next 30 years due to rapid urbanization. Currently, the world generates over two billion tons of municipal solid waste annually. Without immediate action, this could escalate to 3.4 billion tons by 2050. To highlight the awaiting consequences, the World Bank notes that,
In 2016, the world generated a whopping 242 million tonnes of plastic waste. We could make about 24 trillion plastic bottles out of it. Their water volume could fill up 4.8 million Olympic-size swimming pools.
Compounding the challenge, many countries lack the capacity to effectively manage this waste, leading to widespread mismanagement.
Think about it this way: In the long run, the cost of addressing these impacts will far exceed the cost of developing and operating adequate waste management systems.
Drive the Change Toward a Sustainable Future
How can we stay ten steps ahead of the eight wastes? It's straightforward: everyone must take responsibility. Ensuring that the land we live on is safe for us, for our families and friends, and for future generations is the biggest task we face today.
Even small steps can have a profound impact on achieving meaningful change. By integrating green practices through Lean methodologies, businesses and individuals can make significant strides toward sustainability without drastic overhauls. For businesses, it might start with initiatives like:
- Implementing a carpooling program, reducing emissions and fostering team collaboration.
- Offering incentives for employees who carpool, take public transit, or bike to work.
- Subsidizing bus passes to encourage the use of public transportation.
- Allowing employees to work from home a few days a week to cut down on commuting emissions.
Individuals can also play a vital role by adopting actionable practices:
- Trying a meatless day once a week to reduce environmental impact. (If every American cut meat out of their diet even once a week, it would be the equivalent of taking 60 million cars off the road!)
- Gradually eliminate plastic from daily kitchen use.
- Shop at thrift stores when possible, and donate your unwanted items rather than throwing them away.
- Buy your staples in bulk.
Implementing these practices today means seeing long-lasting green efforts as early as tomorrow. By incorporating Lean Six Sigma principles of streamlining waste and maximizing efficiency, both businesses and individuals can move closer to achieving operational excellence through a positive environmental impact.
Going Lean Can Help You Go Green
By uniting lean methodologies and sustainability, we can forge a unified approach that not only improves your business' bottom line but also significantly reduces the environmental impact of your operations. By emphasizing waste reduction, optimizing resource use, and nurturing continuous improvement, businesses can make significant strides in shrinking their ecological footprint starting today.
To illustrate our continued commitment to sustainability, at MoreSteam, we deeply appreciate the incredible work nonprofit organizations do worldwide. To support these efforts, we offer training grants to nonprofits committed to greening their processes. As part of the application process, we ask that you undertake a Green Lean Six Sigma project. Upon completion, we encourage you to share your insights and lessons learned, helping other organizations contribute to a greener world. Contact us to apply!
It’s pivotal that we confront the challenges of our ever-evolving world; deciding whether or not to participate is deciding if future generations will inherit a healthy environment or face the environmental challenges of our making.
This is not merely a choice; it’s a responsibility that begins today.
Additional Resources:
- To read more about MoreSteam’s sustainability goals, check out our page, “Green Lean Six Sigma”.
- For information regarding a company that’s taken significant steps towards promoting sustainability, check out our partner, Ernst & Young's podcast, “Sustainability Matters”.
- For more practical ways to better your sustainability practices in everyday life, take a look at “Greenpeace’s Guide to Life”.

MoreSteam