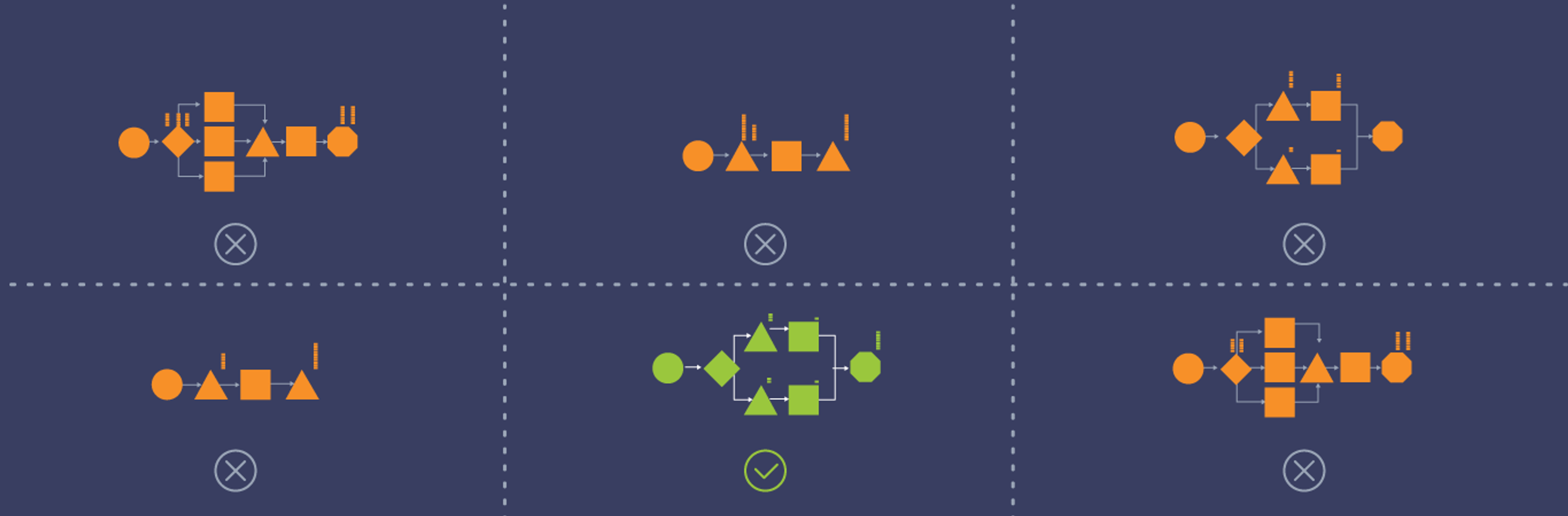
Lean Six Sigma Success Stories: Transforming Processes with Discrete Event Simulation
February 20, 2025Success stories are more than just numbers—they’re proof of what’s possible. Discover how organizations used Lean Six Sigma with discrete event simulation (DES) to overcome challenges, enhance efficiency, and drive operational excellence, all before making a single change in the real world.
This blog explores three compelling Lean Six Sigma success stories that reveal the transformative power of process modeling software, like MoreSteam’s Process Playground. By virtually testing and optimizing processes, these organizations achieved remarkable results without costly trial and error. From complex workflows to high-demand environments, these success stories showcase the potential of integrating Lean Six Sigma methodologies with advanced simulation tools to achieve operational excellence.
New to discrete event simulation? Learn the basics in our blog post: What is Discrete Event Simulation?
Improving Efficiency in Medical Device Manufacturing
Medtronic, a global leader in medical device manufacturing, faced increasing demand for its vessel-seal dissectors, critical tools in laparoscopic surgeries. Traditional value stream mapping revealed inefficiencies, but staple Lean metrics like average cycle time failed to uncover the true source of variation. To overcome this limitation, the team turned to MoreSteam's Process Playground to build a virtual model of the production process.
By simulating variations within process steps and across shifts, the team uncovered bottlenecks that were limiting labor utilization and throughput. Testing potential solutions virtually, they ruled out expensive options like duplicating production lines. Instead, they focused on reducing variation and stabilizing processes, leading to an 11.6% increase in output without additional capital expenditures. In another project, similar modeling efforts nearly doubled output and increased utilization rates from 70% to 98%.
Medtronic’s experience underscores the value of simulation as a Lean Six Sigma tool for achieving operational excellence in regulated, high-stakes industries.
Read the full case study here: Process Modeling Fuels Operational Excellence in High-Stakes Industry
Enhancing Customer Experience in Fast-Casual Dining
A fast-casual pizza chain committed to speed, individuality, and value faced operational challenges during peak hours. Extended queue times threatened customer satisfaction and employee morale. Initial solutions, such as replacing ovens with larger ones, proved cost-prohibitive and disruptive. Instead, the chain collaborated with Service Physics and leveraged Process Playground to create a virtual model of its pizza assembly process.
The simulation revealed that reconfiguring the assembly line, rather than replacing equipment, could significantly improve throughput. By implementing dedicated workstations (“pods”) and eliminating batch processes in the oven, the chain reduced queue times by 33% and increased throughput by 16 pizzas every 30 minutes. Additional changes, such as reorganizing the Expo station and introducing standard work routines, ensured an even flow throughout the operation.
The result was a streamlined customer experience, reduced employee motion, and higher satisfaction across the board. This case highlights how DES enables data-driven decisions that align with Lean Six Sigma’s emphasis on eliminating waste and improving flow.
Read the full case study here: Process Modeling Produces Transformational Recipe for Success
Reducing Queue Times for COVID-19 Testing in Healthcare
At the height of the COVID-19 pandemic, a world-renowned research hospital faced a critical challenge. With thousands of employees returning to work, they needed an efficient screening process to ensure safety without jeopardizing productivity. The initial process, with 10 screening stations, resulted in an average queue time of two hours for over 1,000 employees per day. The backlog led to lost productivity and compromised safety protocols due to overcrowding.
Using Lean Six Sigma principles, the team first applied Heijunka to level the demand by staggering arrival times. However, the high variability in process times and arrival rates meant this alone was insufficient. Enter discrete event simulation. By modeling the process, including triangular distributions for screening times and Poisson arrivals, the team identified the optimal staggered arrival schedule and staffing levels.
The results were transformative: average queue times dropped to nearly zero, productivity losses were eliminated, and social distancing was maintained. The hospital avoided significant capital expenses, relying instead on simulation insights to optimize the existing process. This rapid process prototyping highlighted the power of combining Lean Six Sigma with DES to address urgent challenges.
Read the full case study here: The Impact of Process Modeling: Reducing Queue Times for COVID Testing
Key Takeaways and Real-World Impact of Lean Six Sigma Success Stories
These Lean Six Sigma success stories showcase the transformative power of combining robust methodologies with advanced tools like discrete event simulation. But beyond the compelling narratives, there are valuable lessons and measurable impacts that can be applied to your own process improvement initiatives.
Lessons Learned: Turning Insights into Action
Each success story demonstrates the strategic advantages of using Lean Six Sigma with discrete event simulation:
- Understanding Variability: Variability analysis played a crucial role in optimizing workflows, whether it was reducing queue times or increasing throughput. This highlights the importance of considering real-world fluctuations in process times and demand patterns.
- Rapid Prototyping and Scenario Testing: By creating virtual models, teams were able to test multiple solutions without disrupting actual operations. This rapid prototyping approach accelerated decision-making and minimized risk.
- Data-Driven Decision Making: Lean Six Sigma, combined with DES, enabled data-driven insights that went beyond traditional process mapping, driving more informed and impactful changes.
Quantifying the Benefits: Why Discrete Event Simulation Matters
The real-world impact of using discrete event simulation is not just in qualitative improvements but also in measurable gains, including:
- Reduction in Cycle Times: For example, reducing queue times to nearly zero in the healthcare setting not only improved patient experience but also eliminated productivity losses.
- Increased Productivity and Utilization: In manufacturing, simulation insights led to an 11.6% increase in output and a 28% improvement in labor utilization without additional capital expenditures.
- Cost Savings and ROI: By optimizing existing processes and avoiding unnecessary investments, organizations achieved significant cost savings and maximized ROI.
These quantifiable results underscore the power of combining Lean Six Sigma methodologies with advanced simulation tools. Whether you’re looking to optimize a complex workflow, enhance operational efficiency, or drive strategic growth, discrete event simulation provides a proven, data-driven approach.
Create Your Own Success Story
Ready to achieve similar results? Explore all of EngineRoom’s tools, including Process Playground, and discover how you can leverage discrete event simulation and process modeling to revolutionize your continuous improvement efforts.
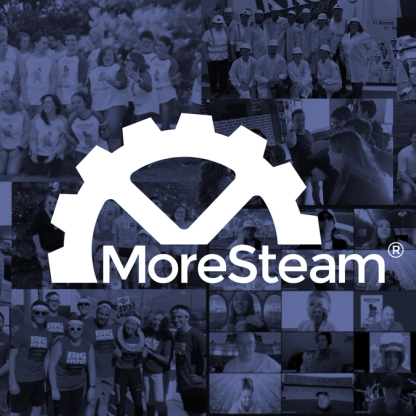
MoreSteam's Enterprise Process Improvement platform includes the tools, training, and software you need to transform your organization, large or small, into a problem-solving powerhouse. Our products are trusted by over half of the Fortune 500 and by other organizations and universities worldwide. When you partner with MoreSteam you gain a team dedicated to helping you succeed.