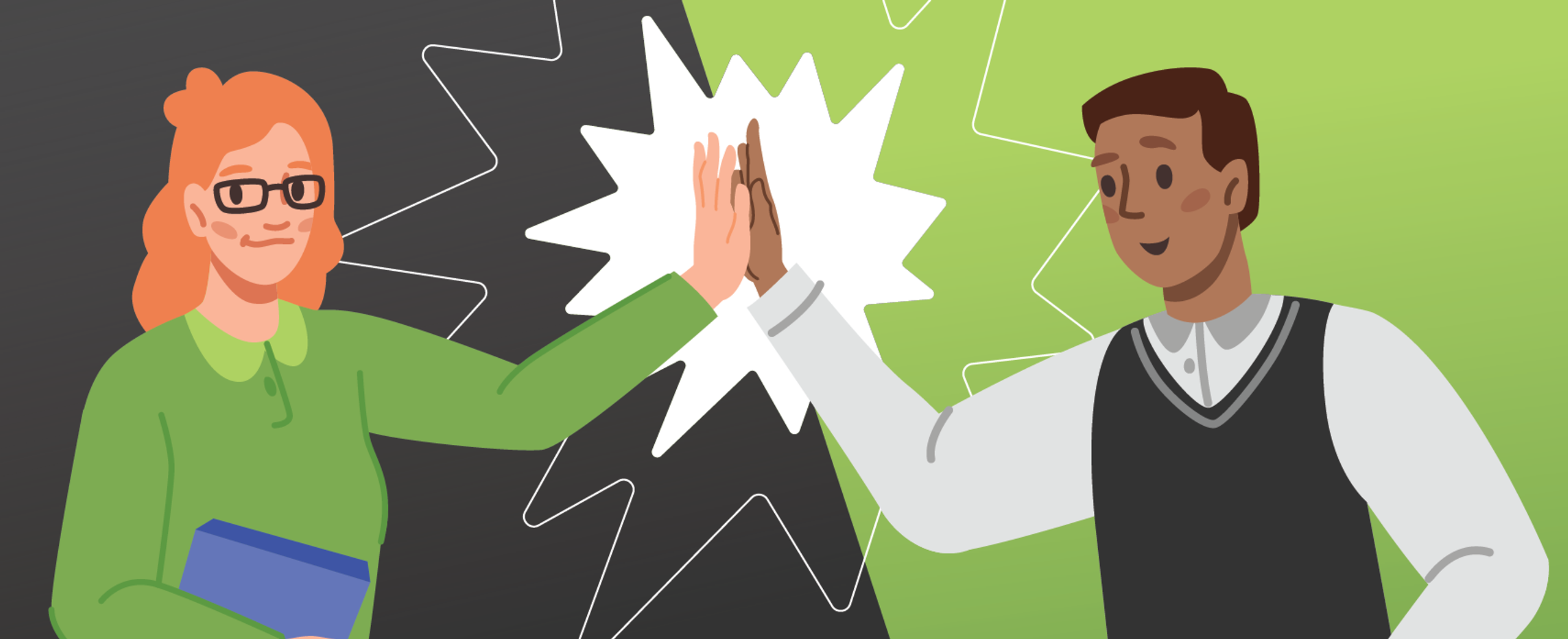
Lean Six Sigma Green Belt vs. Black: Defining the Difference
June 17, 2024When an organization establishes a culture of continuous improvement, it’s imperative that everyone adopts a problem-solving mindset. Pursuing a Lean Six Sigma belt, whether Green Belt or Black Belt, means embracing this culture of change and playing a key role in the bigger picture.
Having multiple individuals of each belt reinforces an organization's operational excellence initiatives and helps balance the knowledge, insight, and tools across all levels of the organization.
Think of it like a movie set: having a director is essential, but a successful production relies on a full crew working together. It wouldn’t make sense to only have directors on set—the movie would never get made. Similarly, Lean Six Sigma projects need a team with a mix of skills and roles to keep everything running smoothly. Just as the director, camera crew, and production assistants all contribute to the final product, Green Belts and Black Belts bring complementary strengths to achieve the organization’s goals.
Choosing the right belt level is like choosing your role on set. Each serves an important purpose, and the best choice depends on where your skills and interests fit into the larger mission.
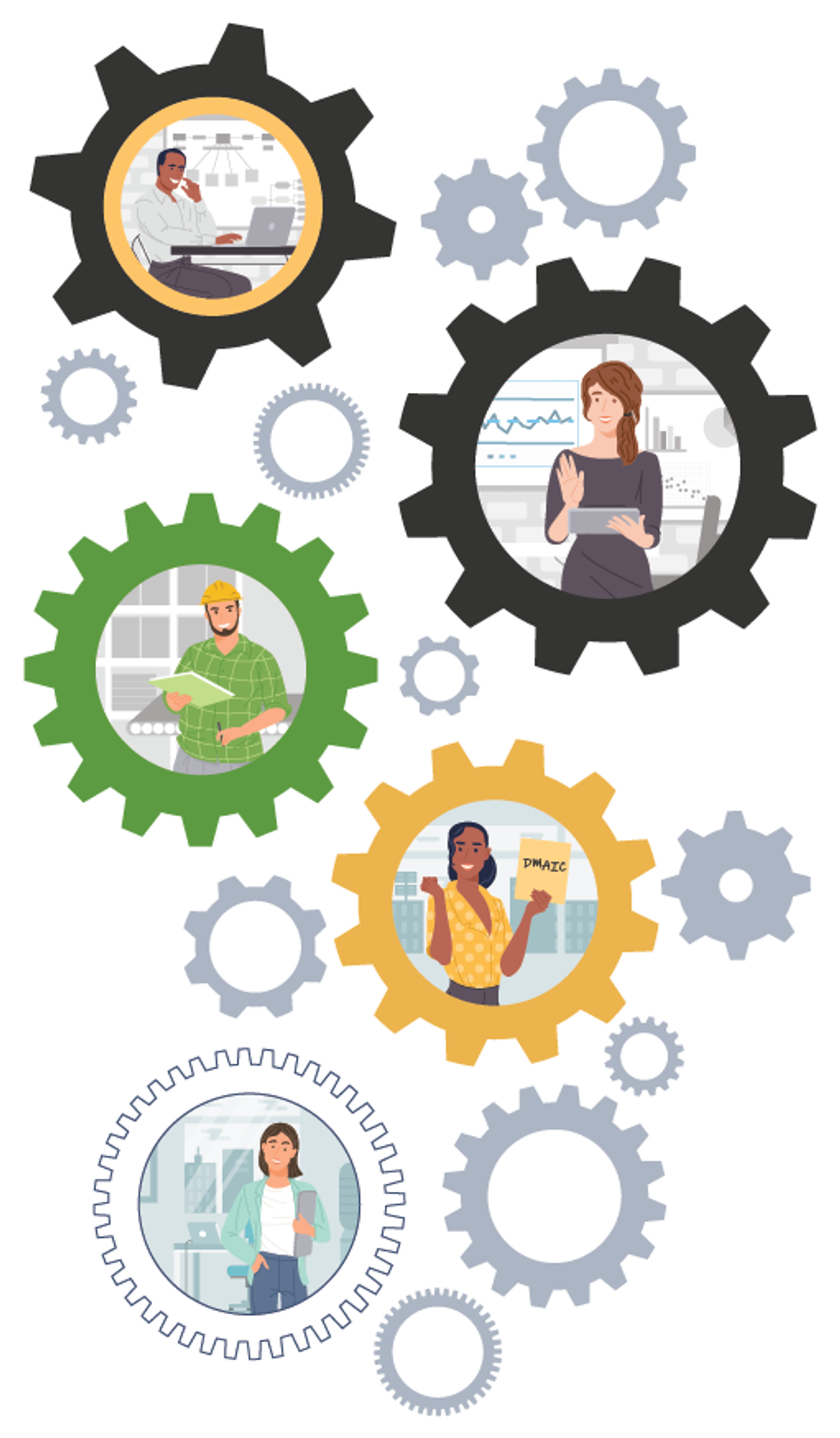
The Hierarchy of Lean Six Sigma Belt Levels
Lean Six Sigma offers training at distinct levels, or "belts." Like the belt levels in karate, each progression comes with more advanced knowledge, training, and skills. The various belt levels that you can earn are as follows:
For a rundown of each of these belts, check out our blog, "Lean Six Sigma Belt Levels Explained."
Each level is meaningful, but two of the most common belts are Green Belt and Black Belt. Choosing which belt level to pursue depends on your personal interests, career goals, and specific job responsibilities.
What’s the Difference Between a Lean Six Sigma Green Belt and a Black Belt?
A Lean Six Sigma Green Belt is a trained professional skilled in Lean Six Sigma methodologies and tools, typically focusing on smaller-scale projects or assisting Black Belts on larger, cross-functional initiatives. Green Belts use the DMAIC method to identify and reduce waste, enhance efficiency, and maintain quality within their specific area or department. Their role is often operational, working to optimize processes within their existing realm of influence.
In contrast, a Lean Six Sigma Black Belt possesses an advanced level of training and a deeper understanding of Lean Six Sigma tools, with a strong focus on statistical analysis and data-driven decision-making. Black Belts lead larger, organization-wide projects that often require collaboration across departments. They are tasked with tackling complex issues, making strategic improvements, and often moving between departments to address high-priority challenges. Black Belt training involves significantly more time and a focus on leadership skills, preparing them for roles in project management and organizational change.
While both Green Belts and Black Belts share a commitment to continuous improvement, the major distinctions lie in the scope of their projects, the depth of their expertise, and their role within the organization. Green Belts concentrate on department-specific enhancements, while Black Belts are strategic leaders driving transformative changes across the organization.
Lean Six Sigma Green Belt vs. Black Belt: The Certification Process
While Green Belt and Black Belt certifications follow a similar format, each focuses on developing different skill sets. It’s important to note that there is no universal standard for either certification, so requirements can vary by program. Below, we outline the certification process for each belt according to MoreSteam’s standards, which emphasize the practical application of DMAIC through project work.
Green Belt Certification
To achieve Green Belt certification through MoreSteam, you must:
- Complete the 80 hours of online training
- Receive a passing score (80% or higher) on the final examination
- Complete one Green Belt project for review
Green Belt training builds on Yellow Belt material, equipping participants to lead their own DMAIC projects. This certification is ideal for those looking to take on project leadership roles in process improvement. In addition to DMAIC skills, Green Belt training includes basic leadership skills for managing small project teams, often with the support of other Green Belts or Yellow Belts. Green Belts also gain a foundational knowledge of statistics for more in-depth analysis.
Black Belt Certification
To achieve Black Belt certification through MoreSteam, you must:
- Complete the 140 hours of online training
- Receive a passing score (80% or higher) on the final examination
- Complete two Black Belt projects for review
Black Belt certification delves deeply into advanced concepts, including root cause identification, process behavior analysis, and complex process improvement projects. Black Belts are prepared to lead high-impact projects that involve statistical analysis or Design of Experiments (DOE). They also mentor Green Belts and serve as key experts in process analysis and optimization across their organizations.
Lean Six Sigma Green Belt vs. Black Belt: Core Competencies
Each belt level signifies a deeper understanding and proficiency in Lean Six Sigma methodologies. Many of the skills and tools you may learn as a Green Belt are then built upon and expanded as a Black Belt.
Green Belt Core Competencies
As a Green Belt, some of the key skills you can expect to gain a basic understanding of include:
- Data collection and analysis
- Basic project management for smaller projects
- Root cause analysis
- Process mapping
- Six Sigma Methodology
- Problem-solving techniques
- Lean principles and waste elimination
- Critical thinking skills
- Communication and leadership skills
- Change management
- Quality control
Black Belt Core Competencies
As a Black Belt, you will build upon the foundational skills and tools acquired as a Green Belt, deepening your expertise and mastering more complex applications. This advanced skill set includes:
- In-depth knowledge and application of DMAIC and DFSS (Design for Six Sigma) for complex problem-solving and process design
- Expert use of advanced statistical tools and software for data analysis
- Sophisticated problem-solving techniques for complex and large-scale process improvement projects
- Managing larger, more complex projects with multiple teams and cross-functional stakeholders
- Deep understanding and application of Lean principles to drive significant efficiency improvements
- Creating detailed process maps and conducting value stream mapping for thorough process analysis
- Developing strategic thinking skills for long-term process improvement and organizational growth
- Advanced leadership and communication skills to lead large teams, mentor Green Belts, and influence organizational change
- Expertise in change management techniques to implement major process changes and drive cultural transformation
- Advanced knowledge of quality management systems and regulatory standards
- Proficiency in advanced root cause analysis techniques and tools (e.g., FMEA, Fishbone diagrams)
- Understanding of financial impact analysis and cost-benefit analysis to justify and measure project success
- Advancing your skills to coach and mentor Green Belts and other team members
Lean Six Sigma Green Belt vs. Black Belt: Typical Project Work
There’s significant overlap in the types of projects Green Belts and Black Belts handle. Regardless of level, process improvement projects typically focus on similar goals, such as reducing waste and increasing efficiency. The main difference lies in the complexity of the problems tackled and the level of responsibility each role carries.
Here are examples of projects you might work on, highlighting the differences between a Green Belt and a Black Belt’s approach:
Process Improvement in Manufacturing
- Green Belt Role: Focus on analyzing and enhancing specific steps within the manufacturing process to reduce defects and improve efficiency.
- Black Belt Role: Lead large-scale improvement projects by developing the project charter, defining goals, mentoring Green Belts, and coordinating cross-functional teams to align with organizational objectives.
- Real-World Example: Explore how Medtronic used Lean Six Sigma principles to revamp its value stream maps and drive manufacturing process improvements.
Customer Service Enhancement
- Green Belt Role: Streamlining specific customer service processes to reduce wait times and improve satisfaction.
- Black Belt Role: Identifying strategic opportunities for improvement, conducting high-level data analysis, guiding the implementation of solutions across multiple customer service touchpoints, and ensuring long-term sustainability.
Supply Chain Optimization
- Green Belt Role: Improving inventory management or supplier performance.
- Black Belt Role: Leading a comprehensive supply chain optimization project, developing strategies for supplier integration, and ensuring that improvements align with broader supply chain and business objectives.
Healthcare Process Improvement
- Green Belt Role: Reducing patient wait times or improving billing processes.
- Black Belt Role: Overseeing the entire healthcare process improvement initiative, using advanced statistical tools to analyze data, working closely with senior healthcare administrators, and ensuring compliance with regulatory requirements.
- Real-World Example: Explore how a healthcare team applied these principles in a real-life hospital process improvement project.
Transactional Process Improvement
- Green Belt Role: Streamlining specific transactional processes like accounts payable or data entry.
- Black Belt Role: Leading enterprise-wide transactional process improvements, mentoring Green Belts, utilizing advanced process mapping techniques, and ensuring the integration of improvements with other business processes.
Quality Improvement in Service Industries
- Green Belt Role: Focus on specific operational improvements, such as reducing order errors or streamlining back-office tasks to increase efficiency.
- Black Belt Role: Lead a broad quality improvement initiative, using Six Sigma methodologies to identify and address root causes of inefficiencies in the service process and ensuring alignment with customer satisfaction goals. This might include re-evaluating workflows, optimizing resource use, or implementing quality control measures.
- Real-World Example: See how Service Physics used process modeling to tackle order processing challenges and improve customer experience.
Project Management
- Green Belt Role: Implementing better project tracking and reporting systems.
- Black Belt Role: Leading the project management improvement initiative, developing standardized project management frameworks, mentoring project managers, and ensuring that improvements are scalable across the organization.
Operational Efficiency
- Green Belt Role: Reducing downtime in machinery or optimizing warehouse operations.
- Black Belt Role: Leading large-scale operational efficiency projects, using advanced Lean tools to identify and eliminate waste and ensuring that efficiency improvements are integrated into the organization’s strategic goals.
As a Green Belt, much of your project work will focus on using the DMAIC method to drive and sustain improvements. As a Black Belt, your role expands to include strategic planning, advanced data analysis, project leadership, and mentoring, ensuring that improvements are implemented effectively, sustained over time, and aligned with the organization’s broader goals.
Which Certification is Right for You?
Choosing the right belt level can greatly enhance your career, no matter which path you take. The decision ultimately depends on your interests, ambition, role, and responsibilities.
Green Belt training is an excellent option for process or manufacturing engineers, continuous improvement specialists, and project managers looking to boost their skills. Black Belt training, on the other hand, is ideal if you’re aiming for senior leadership, a director role, or high-level project management. Think about your current job, career aspirations, and the skills you want to develop to decide which certification aligns best with your goals.
Remember, Lean Six Sigma training requires time and dedication to master. You might choose to start at a lower level and progress over time—both Green and Black Belts add significant value to your career and organization.
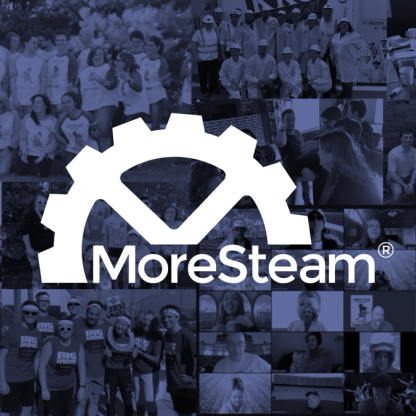
MoreSteam's Enterprise Process Improvement platform includes the tools, training, and software you need to transform your organization, large or small, into a problem-solving powerhouse. Our products are trusted by over half of the Fortune 500 and by other organizations and universities worldwide. When you partner with MoreSteam you gain a team dedicated to helping you succeed.