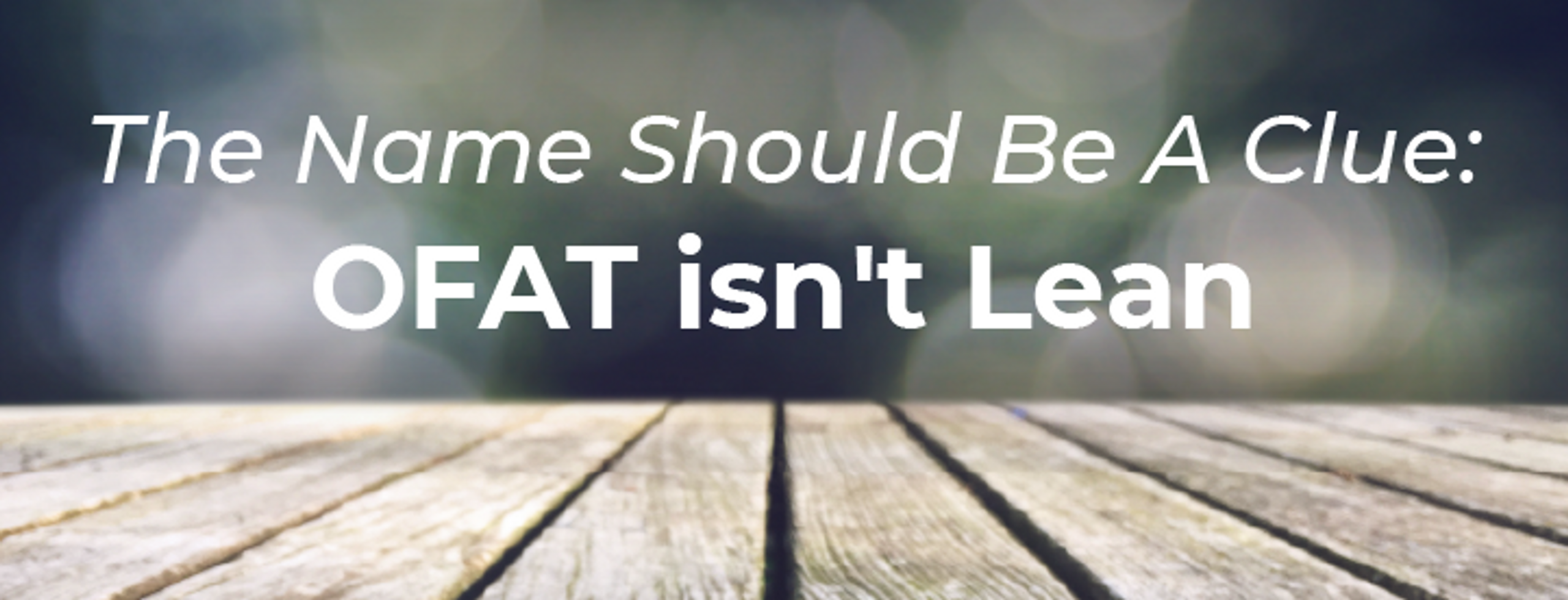
Complex Solutions May be the Leanest Ones
February 22, 2019While eating my lunch at the park last fall, I looked down at the wooden deck below me, and noticed that an ant had picked up a large crumb from my sandwich. The crumb was heavy, and the ant labored to move it. Unfortunately, the gap between the deck planks was too wide for the ant to cross while toting his new-found feast.
The problem is that the ant didn't have any perspective on the problem. He couldn't look down the length of the gap to see if there was a narrow spot, so he was forced to experiment, one step at a time.
It was a practical approach to problem-solving—a methodical one-factor-at-a-time (OFAT) effort that was necessary given the ant's physical limitations, but certainly not very efficient. I was struck by the parallel to our world of process improvement.
The Lean approach prizes many small incremental steps toward continuous improvement. The advantage is simplicity. Those small incremental steps can be carried out without computational complexity, and with limited risk. But it can take a long time to get from here to there along a winding path—not really a Lean process when you think about the wasted time and effort.
If the ant could have seen his problem from a larger perspective, he would have noted that the gap between planks was not uniform and that there was an opportunity to cross the deck with only a short walk. This is what sound experimental design allows us to do: stand back to identify the best path while expending the least resources to do so.
Consider the current state of A/B testing (often used to evaluate how customers react to alternate website designs) — a quick method to compare one factor level to another. A/B testing is easy to set up and interpret, but as a form of OFAT experimentation, it only answers questions about main effects, and does so in an inefficient fashion. More importantly, it doesn't provide the insights about the factor interactions that might be really useful to understand.
Eventually, the ant found the narrow spot, and was able to cross over with the bread crumb, but it took a long time, a lot of trial and error, and he had to cover a lot of ground. It's a good lesson for us.
On occasion, we see a bit of "Sigmaphobia" on the part of Lean practitioners, and I think it's misplaced. Yes, traditional Six Sigma tools can over-complicate a simple problem, and yes, Lean methods are great for engaging the workforce in a culture of improvement, but sometimes, more complex tools are a much Leaner way to arrive at the optimal solution. There's plenty of need for a robust blending of approaches.
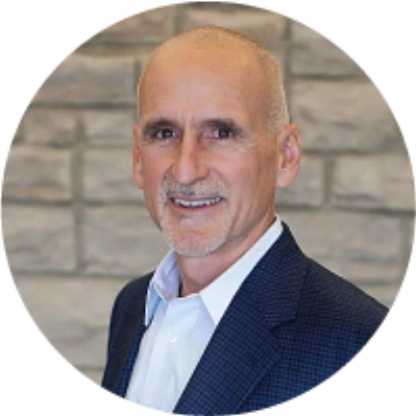
CEO • MoreSteam
MoreSteam is the brainchild of Bill Hathaway. Prior to founding MoreSteam in 2000, Bill spent 13 years in manufacturing, quality and operations management. After 10 years at Ford Motor Co., Hathaway then held executive level operations positions with Raytheon at Amana Home Appliances, and with Mansfield Plumbing Products.
Bill earned an undergraduate finance degree from the University of Notre Dame and graduate degree in business finance and operations from Northwestern University's Kellogg Graduate School of Management.